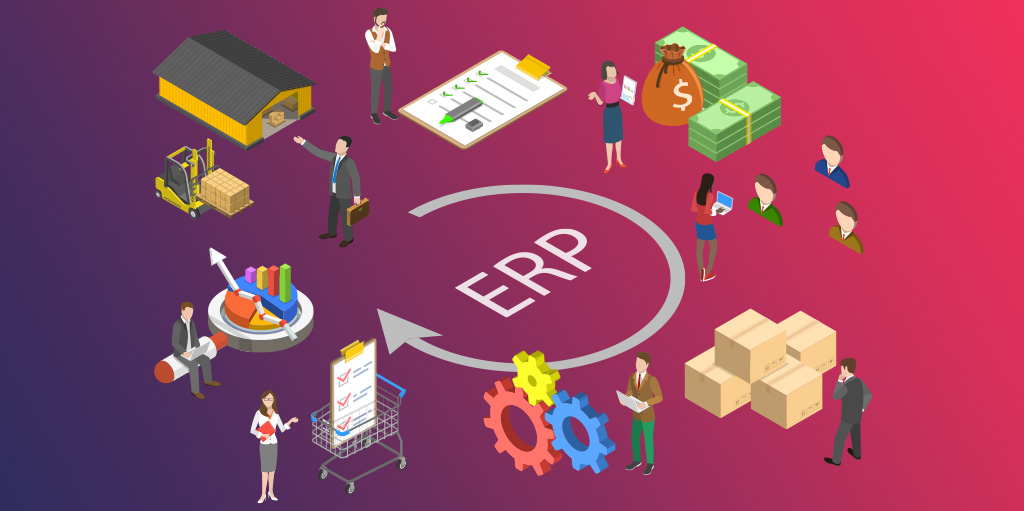
¿Qué distingue a un ERP de manufactura de otros sistemas ERP?
Todos estamos familiarizados con los sistemas ERP: soluciones de software que reúnen todos los procesos empresariales centrales en una base de datos, eliminando ‘islas de información’ e integrando a los distintos departamentos de la organización. Funcionan en tiempo real y tienen una apariencia y un aspecto coherentes en todas las aplicaciones.
Los sistemas ERP nacieron en la industria de manufactura, pero poco a poco se fueron expandiendo a otros mercados.
Muchos proveedores de ERP construyeron sus sistemas exclusivamente para las áreas de finanzas y contabilidad, algunos para la gestión de almacenes y cadenas de suministro; muchos para gobiernos y organizaciones sin fines de lucro, entre otros.
La mayoría de las funciones de “front-office”, como la gestión de relaciones con el cliente (CRM), el comercio electrónico, la gestión de la cadena de suministro (SCM) y la inteligencia empresarial (BI) se agregaron a partir del año 2000, ya que internet permitió la interconexión y el acceso a empleados, clientes y vendedores.
Todas las organizaciones necesitan implementar los módulos principales: Contabilidad General, Cuentas por Pagar, Cuentas por Cobrar, Nómina y Recursos humanos (RH).
Las organizaciones comerciales, aquellas que solo compran y venden, necesitan implementar las funciones de órdenes de venta, órdenes de compra, inventario y administración de la cadena de suministro.
Los fabricantes necesitan todas estas funciones, pero también necesitan mucho más.
¿Desea una DEMO gratis, conocer más sobre nuestros productos o simplemente hablarnos sobre sus necesidades productivas?
CONTÁCTENOS AQUÍ.
Definición de ERP de manufactura
Entonces, ¿qué impacto tienen los softwares ERP de manufactura actualmente?, ¿Qué ofrecen los proveedores el día de hoy?
Actualmente, los productores son diferentes. No construyen edificios, no administran gobiernos ni ONGs, no compran y venden sin agregar valor. Agregar valor es la gran diferencia. Los fabricantes compran materiales y los convierten en productos rentables.
Los fabricantes pueden operar de las siguientes formas:
- Pueden producir por pedidos específicos de clientes (make to order).
- Pueden producir anticipadamente para pedidos que están por llegar (make to stock).
- Pueden fabricar productos personalizados de acuerdo a los requisitos del cliente.
Independientemente del modelo de producción, todos los fabricantes comparten un proceso similar que genera 8 grandes preguntas que necesitan respuestas.
Una vez que las órdenes de venta se acumulan, un fabricante tiene muchas preguntas que deben formularse y responderse:
- ¿Qué necesito hacer?
- ¿Cuándo necesito hacerlo?
- ¿Cómo lo hago?
- ¿Qué necesito comprar para hacerlo?
- ¿Qué recursos necesito tener disponibles para hacerlo?
- ¿Cómo puedo hacerlo de forma eficiente?
- ¿Este proceso es rentable?
- ¿Cómo aseguro la calidad de los procesos?
Un sistema ERP de manufactura requiere módulos específicos para responder consistentemente esas preguntas:
- Lista de materiales y enrutamiento
- Gestión de inventario
- Programación maestra de producción (MPS)
- Planificación de necesidades de material (MRP)
- Planificación de los requisitos de capacidad (CRP)
- Planificación Avanzada y Programación (APS)
- Gestión de producción
- Apoyo para la recopilación automatizada de datos
- Integración con línea de producción
- Movilidad
- Control de Calidad
La funcionalidad de Lista de Materiales puede requerir la integración de aplicaciones de diseño como el software CAD / CAM. Los fabricantes, en particular los que se dedican al mercado de bienes de consumo, adoptan frecuentemente alguna forma de gestión del ciclo de vida del producto.
Para cada pregunta, un módulo del ERP tiene una respuesta
Cuando las órdenes de venta de los clientes se registran en un sistema ERP de manufactura, se suman en la Programación Maestra de Producción para responder la primera pregunta, ¿qué debemos hacer? El MPS puede combinar pedidos del mismo producto.
Como cada pedido de venta tiene una “fecha de solicitud”, también sabemos inicialmente cuándo tenemos que hacer los productos para cumplir con la fecha de entrega solicitada por el cliente. Esto, por supuesto, supone que tenemos capacidad ilimitada en nuestra planta y recursos ilimitados para hacer lo que se necesita. Eso sería una planta extremadamente ineficiente.
Debido a que todo lo que se hace en esos pedidos de venta debe hacerse, necesitamos algo que nos diga cómo se deben hacer. Ese algo es la Lista de materiales (BOM), que es mucho más que una simple lista. De hecho, la Lista de materiales impulsa casi todo a partir de este punto. En su nivel más básico, una lista de materiales con sangría es una vista del producto que muestra cada subconjunto y las piezas necesarias para hacer cada uno de ellos, todo enrollado hasta el ensamblaje final: el producto vendible.
El enrutamiento funciona junto con la lista de materiales. El enrutamiento nos indica el orden en que se hacen los subconjuntos, en qué máquinas se pueden hacer, qué habilidades se requieren para operar esas máquinas y mucho más.
Un aspecto realmente importante del enrutamiento es el tiempo que demora la fabricación de piezas o subconjuntos en cada máquina o centro de trabajo. Esta es su capacidad, es decir, el rendimiento en el tiempo. La planificación de la capacidad nos indica la carga en cada máquina y dónde se producen los cuellos de botella.
Se pueden utilizar rutas alternativas para extender la carga o reducir los cuellos de botella. Dichos cuellos de botella pueden indicar que se debe adquirir una planta adicional o que algunas tareas pueden ser subcontratadas a un fabricante diferente, contratado. La subcontratación también se rastrea a través de una orden de producción vinculada a la compra.
Si desea conocer más sobre nuestro sistema ERP enfocado en manufactura, déjenos estos sencillos datos y lo contactaremos:
Algo bien fabricado, está hecho con eWorkplace.