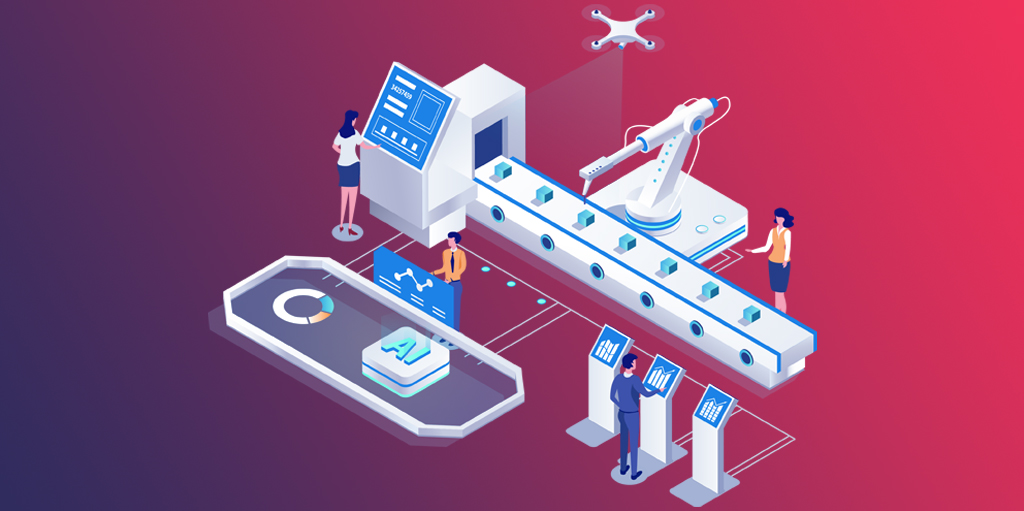
Planeación de requerimientos de materiales
La planeación de requerimientos de materiales (MRP, por sus siglas en inglés) es un procedimiento de computación que se utiliza para convertir el programa maestro de producción de productos finales en un programa detallado de materias primas y componentes que se usan en los productos finales.
El programa detallado indica las cantidades de cada artículo, cuándo debe reabastecerse y cuándo entregarse para cumplir con el programa maestro.
La planeación de requerimientos de materiales es más conveniente para talleres y producción por lotes de diversos productos que constan de múltiples componentes, cada uno de los cuales debe adquirirse o fabricarse. Es la técnica apropiada para determinar cantidades de artículos de demanda dependiente que constituyen los inventarios de manufactura: materias primas, piezas compradas, trabajo en proceso, etcétera.
El concepto de la planeación de requerimientos de materiales (MRP) es relativamente directo. Su aplicación se complica por la magnitud de los datos que se van a procesar. El programa maestro especifica la producción de productos finales en términos de entregas mensuales. Cada producto puede contener cientos de componentes.
El tiempo de entrega de un trabajo es el tiempo que debe permitirse para completar el trabajo desde el principio hasta el final. Hay dos tipos de tiempos de entrega en MRP:
- El tiempo de entrega de pedido. Es el que se requiere desde el inicio de la solicitud de compra hasta que se recibe el artículo del proveedor.
- El tiempo de entrega de manufactura. Es el tiempo que se requiere para producir el artículo en la propia planta de la compañía, desde la autorización del pedido hasta su terminación.
Entradas al sistema de planeación de requerimientos de materiales (MRP)
Para que el procesador MRP funcione adecuadamente, debe recibir varias entradas:
- Lista de materiales. Contiene las piezas de los componentes y los subensambles que forman cada producto. Se usa para calcular los requerimientos de materias primas y componentes utilizados en los productos finales que enlista el programa maestro.
- Se identifica cada artículo (por número de pieza) y proporciona un registro con fases de tiempo del estado del inventario. Esto significa que no sólo se enlista la cantidad actual del artículo, sino los cambios futuros que ocurrirán en el nivel de inventario y cuándo sucederán. Los datos incluyen los requerimientos globales del artículo (cuántas unidades se necesitarán para construir productos en el programa maestro), las entregas programadas, el estado en existencia y las liberaciones de pedidos planeadas. Cada uno de estos conjuntos de datos indican los cambios por periodo de tiempo en el programa (por ejemplo, un mes o una semana).
Con base en la información, el procesador MRP calcula cuántos componentes y materias primas se necesitarán en los periodos futuros, explotando en niveles sucesivos inferiores en la estructura del producto. Los cálculos del MRP deben manejar varios factores complicados. Primero, las cantidades de componentes y subensambles deben ajustarse para los inventarios actuales o solicitados. Segundo, las cantidades de artículos de uso común deben combinarse durante la separación de piezas para obtener un requerimiento de cada componente y materia prima en el programa. Tercero, las entregas en fases de tiempo de productos finales deben convertirse en requerimientos de componentes y materiales en fases de tiempo, factorizando los tiempos de entrega adecuados.
Beneficios de utilizar un MRP:
- Reducciones de inventarios
- Respuesta más rápida a cambios en la demanda
- Costos reducidos de reparación y cambio
- Mejor utilización de las máquinas
- Mayor capacidad de respuesta a los cambios en el programa maestro
- Ayuda en el desarrollo del programa maestro.
A pesar de estas consideraciones, los sistemas MRP se han instrumentado en la industria con diversos grados de éxito. Algunas razones por las cuales no han tenido éxito son:
- Aplicación inadecuada.
- Cálculos de MRP basados en datos imprecisos.
El sistema MRP de eWorkplace Manufacturing le ayuda a la planificación de compras eficiente y la optimización de costos.